All dealers should document equipment inspections on an equipment inspection checklist.
Forklifts, eyewash stations, aerial lifts and fire extinguishers, oh my! This is just a short list of the equipment at the dealership that must be inspected on a routine basis. In a highly regulated state like California, it should come as no surprise that state law requires dealers to routinely inspect their equipment at regular intervals. But aside from the regulatory requirements, routinely inspecting equipment ensures that all equipment meets safety standards, functions efficiently and remains in optimal condition, which is essential for maintaining both employee and customer satisfaction. By identifying potential issues early on, equipment inspections help prevent accidents from occurring, reduce any downtime due to those accidents and avoid repairs that eventually become costly. Keeping track of the various intervals of multiple inspections can be confusing. Here is a list of the most common dealer equipment that requires a routine inspection:
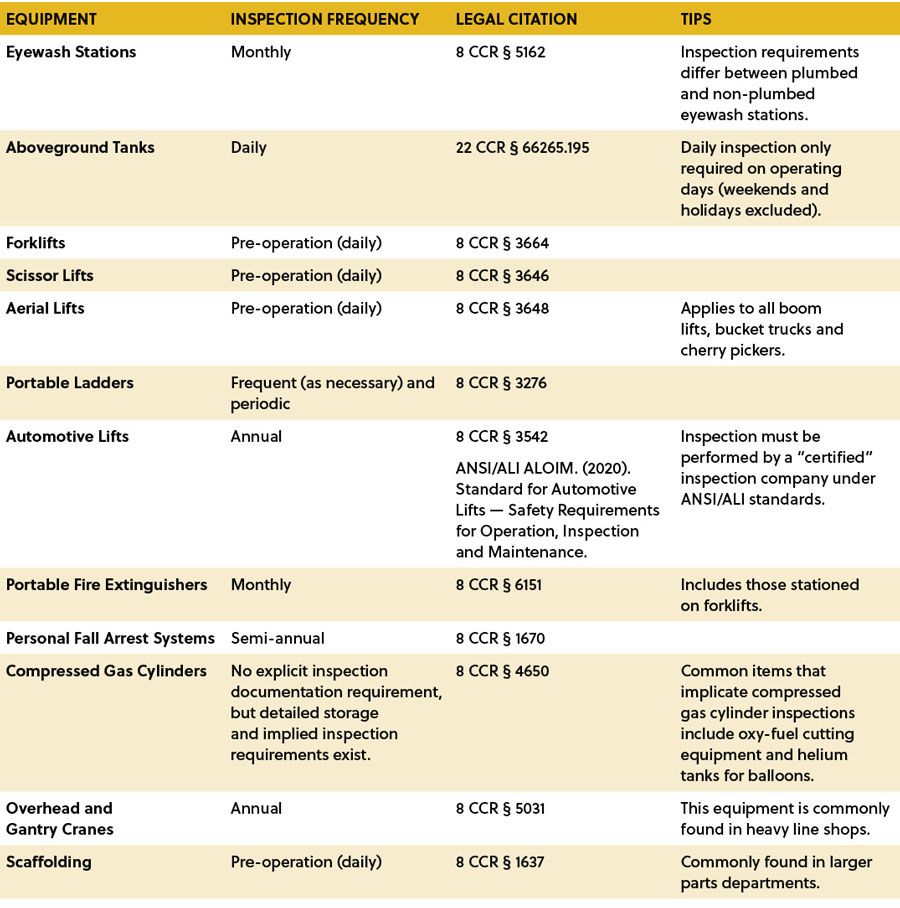
Practical Tips
As we stated above, performing these routine inspections should be a cornerstone of every dealer’s safety program. In fact, most entries on OSHA’s top 10 citations list for 2023 involve equipment requiring regular inspections. Not only should the equipment be inspected on a regular basis, but dealers should adhere to lockout/tagout procedures whenever equipment is in need of service or repairs.
Keep in mind that Cal/OSHA may request to review inspection records if they ever decide to visit your dealership. All dealers should document equipment inspections on an equipment inspection checklist. A checklist documents that employees are inspecting all required equipment components. Paper inspection checklists are a thing of the past; switch to electronic checklists accessible through QR codes posted directly on the equipment. Electronic checklists are durable against time and weather, offering employees easy access through a quick QR scan with an electronic device. This method also allows for electronic notifications for any missed inspections, enhancing efficiency and compliance.
Because there are various pieces of equipment scattered throughout different departments of the dealership, we also recommend that department managers appoint staff to perform the necessary equipment inspections within their departments. Thereafter, the same managers should verify that their staff are completing equipment inspections in a timely manner by occasionally auditing inspection checklists. Think of it as an inspection for the inspection! This type of top-down accountability will help establish a culture of compliance in service and parts departments that will extend beyond equipment inspections and positively benefit the dealership’s overall safety efforts.
Questions?
For more information on how ComplyAuto Safety can assist your dealership in automating your required routine inspections, please contact us at info@complyauto.com.